Brux Barrels, based in Lodi, Wisconsin, has earned a reputation for producing great-shooting tubes. Brux-made barrels have won their fair share of matches, and set some notable records in the process. A few years back, Rodney Wagner shot the smallest five-shot, 600-yard group (0.336″) in the history of rifle competition, using a Brux barrel chambered for the 6mm Dasher. Brux barrels are used by top shooters nationwide, and finish at the top consistently.
Owner Norman Brux has
been in the world of machines since he built his first rifle at 14.
He was trade-school trained as a tool, die and mold maker,
earning his apprenticeship at E. A. Schmid, and honed his
mold-making skills at F. J. Sipos.
Norm move to Wisconsin and
started KNB Tool Company in 1986, and founded Brux Barrels in 2006.
His parents were German immigrants and his father Klaus purchased
rifle-making machinery, aware that vintage equipment was the key to
quality machining. Norm rebuilt and re-engineered these machines to
provide the tolerances necessary for efficient, flexible barrel
fabrication.
His love for the work and the sport make Brux
the barrel of choice for many of the world's finest competition
shooters.
Owner Ken Clemens is a
native of Wisconsin, working on the family farm before beginning a
career with Marshall Erdman's Techline company that spanned 30
years. Ken worked at Techline for many years with Ken
Liebetrau, who left to begin making barrels at Brux. Ken followed
him to Brux, and after Liebetrau's retirement recently, partnered
with Norm as co-owner of Brux Barrels LLC.
Ken's
manufacturing experience, dedication to quality craftmanship and
customer service guarantee that the name Brux
represents the very best custom rifle barrels available.
What's the Secret?
Folks often ask why Brux barrels shoot so well. “What’s the secret?”. To make a cut-rifled barrel you have to start off with the proper ingredients: the best steel available, the best tools in the industry, skill, and experience. Since there are really only two main suppliers of barrel-quality steel, the skill and experience is what really makes a barrel maker stand out. Here is how Norman Brux explains all the procedures involved in making a Brux cut-rifled barrel:
Creating the Masterpiece - Step By Step
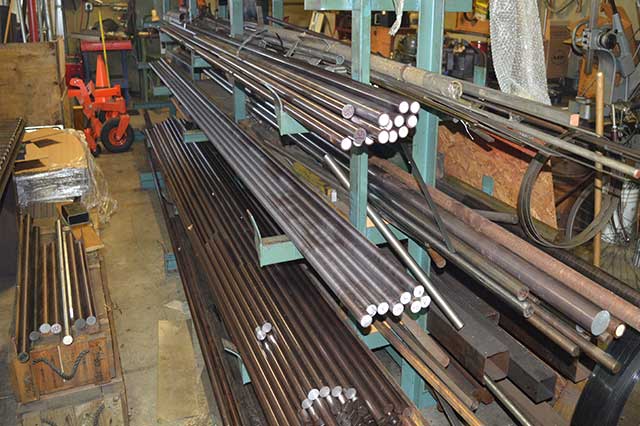
Step One
Material Selection
We start out with either 4150 chromemoly or 416R stainless
steel double stress-relieved stock. The stock starts
out at 1-9/32″ in diameter and 20-24 feet long We
cut to custom lengths per customer specifications.
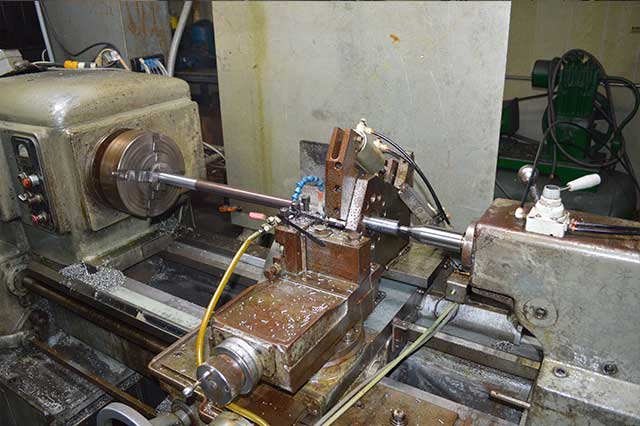
Step Two
Barrel Contouring
The outside of the barrel is turned on a lathe and prepared
for drilling. As in each of the following steps, the barrel
is carefully cleaned after the process.
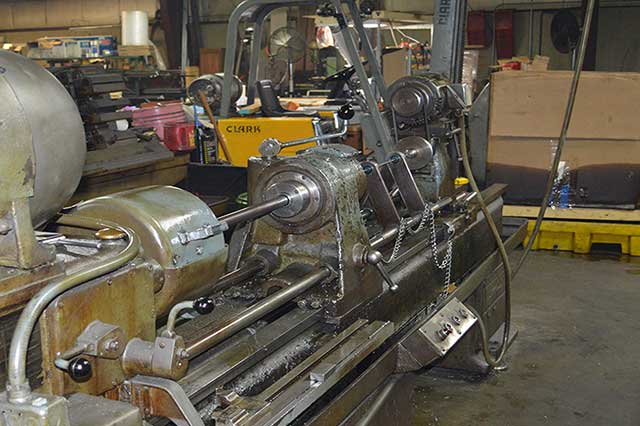
Step Three
Drilling
The cutter bit has holes through which oil or coolant is
injected under pressure to allow the evacuation of chips formed
during the cutting process. This is called “oil-through” or
“coolant-through”. The combination of a 3600 rpm turning speed
and good flushing allows us to drill a beautifully straight
and centered hole .005” under “land” diameter. Cleaning is done
again.
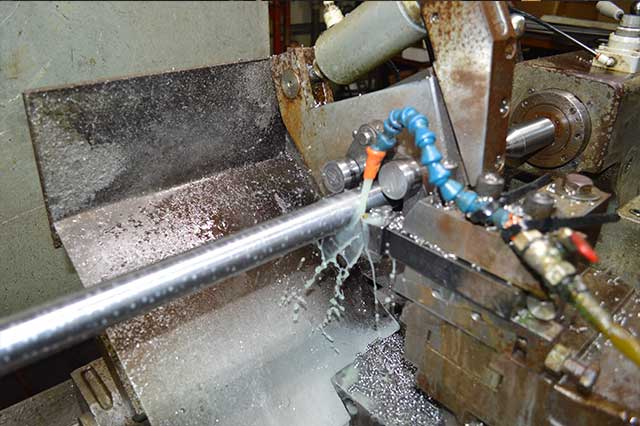
Step Four
Outside Contouring
The barrel is now sent back to the lathe for final contouring
of the exterior. Brux offers a variety of configurations and
the barrel is turned to exacting specifications and finished
to near perfection. A Monarch vintage lathe provides the high
quality of exterior turning, and our expert machinists ensure
that each customer's specs are met exactly. The barrel is cleaned
and prepared for reaming.
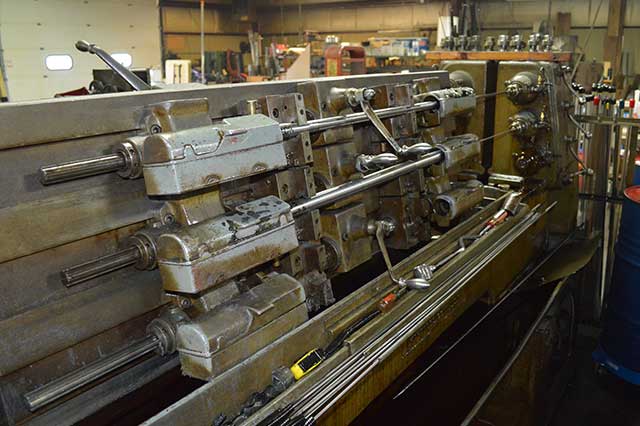
Step Five
Reaming
The blank is then sent to the Pratt and Whitney reamer
in which an “oil through” reaming tool is used to cut away
the extra .005” left in the drilling process. The reamer
makes an extremely accurate bore size ensuring a better
surface finish and the proper “land” diameter.
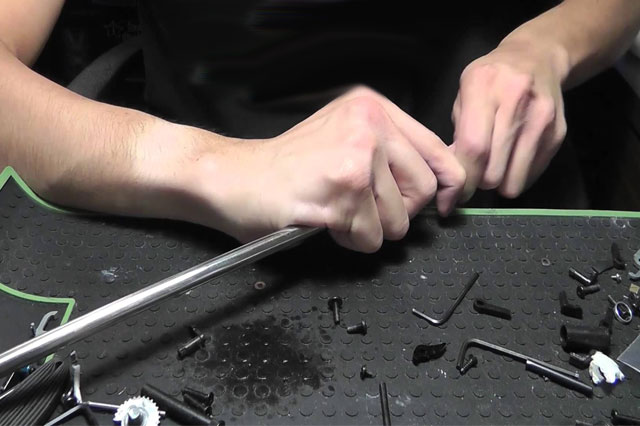
Step Six
Hand Lapping
We hand lap each barrel to remove any slight tool marks
that may have been left by the reamer and inspect every
barrel with a bore scope. If the barrel doesn’t meet our
standards for surface finish and tolerance it is discarded.
Lapping is a finishing process for the interior of the barrel.
We hand lap, as we believe in taking the time and care to
achieve the utmost mirror shine and smoothness of the barrel.
The barrel is cleaned again.
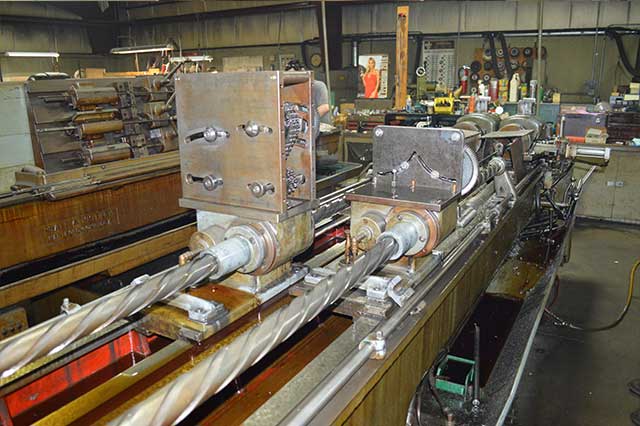
Step Seven
Rifling
The rifling machine is responsible for cutting
the all so familiar grooves in the bore. A caliber/land
configuration-specific rifling head is used to progressively
shave away small amounts of steel to form the rifling grooves.
This is accomplished by simultaneously pulling the rifling
head through the reamed blank as the blank is spun at a
controlled rate. This is the heart of the barrel-making
process, requiring decades of experience and dedication
to the craft.
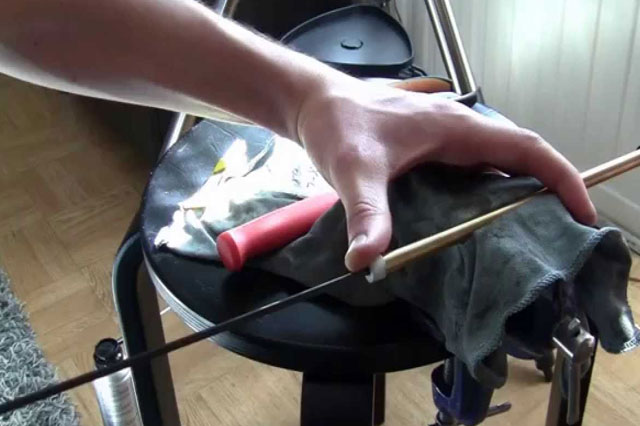
Step Eight
Final Hand Lapping
Lastly, the barrel is hand-lapped again (to ensure a
smooth bore) as the final interior finishing process. This
time-consuming and precision procedure ensures the ultimately
smooth inner surfaces. A final inspection is performed with
the bore scope, then your custom BRUX Barrel is carefully
packed and prepared for shipping. Brux never takes shortcuts.
Every barrel is fabricated in this proven method, and many
critical elements are closely guarded trade secrets, unique
to BRUX.